2015年12月16日,国内首支国和一号发电机半速转轴在二重制造成功,各项质量指标全部达到标准要求。历经一年零三个月的攻坚,二重人品尝到收获的喜悦。
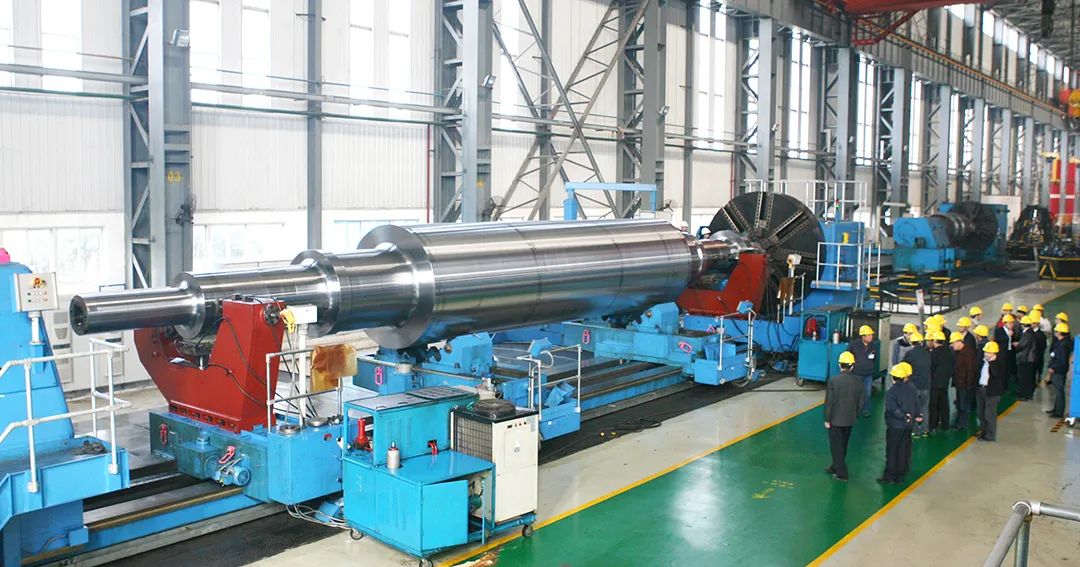
意义重大 要求极高 极限制造
半速转轴是核电的关键锻件之一,也是整个机组中最大的锻件,采用650吨钢锭进行制造,其制造技术难度达到世界同类产品的极限水准,世界上仅有少数国家具备制造能力。对于国内装备制造企业来说,该核电半速转轴就是国家装备制造领域核心技术难题,是必须全力攻克的国产化重点高端大型产品。
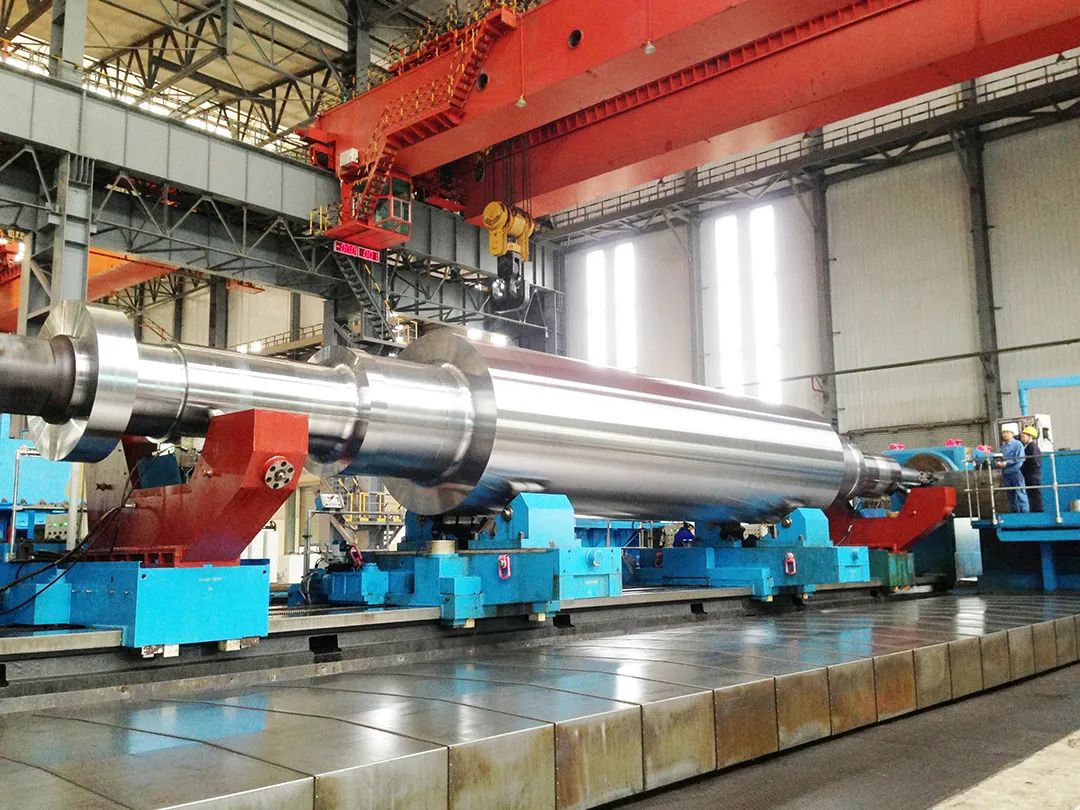
勇担使命 一举成功 打破垄断
从2006年开始,二重组建攻关团队,在国家课题支持下,开展核电半速转轴研制工作,经过创造性的艰苦攻关,完成了特大型锻件极限制造流程创建。同时进行了一系列重大原始创新,掌握了特大型转子全套制造技术,于2010年成功研制了国内首支1000兆瓦级核电半速转子,实现了特大型锻件极限制造能力和技术的重大突破,为高端大型锻件极限制造奠定了基础。陆续又为国内核电站提供了6支1000兆瓦级的核电半速转轴,成为国内特大型核电半速转轴的最大供应商,产品质量水平和制造能力达到国内领先水平。
2013年,二重承制国内首支国和一号转轴。“该产品无论从重量、尺寸、材料力学性能、钢的纯净度和加工精度及所需的制造设备等级,均达到了极限水平。每道工序都面临着很大的风险和严峻考验,一系列的技术难题都需要解决。”二重首席技术专家,同时也是核电半速转轴锻件研制课题负责人谈起产品研制过程时,仍充满感慨。
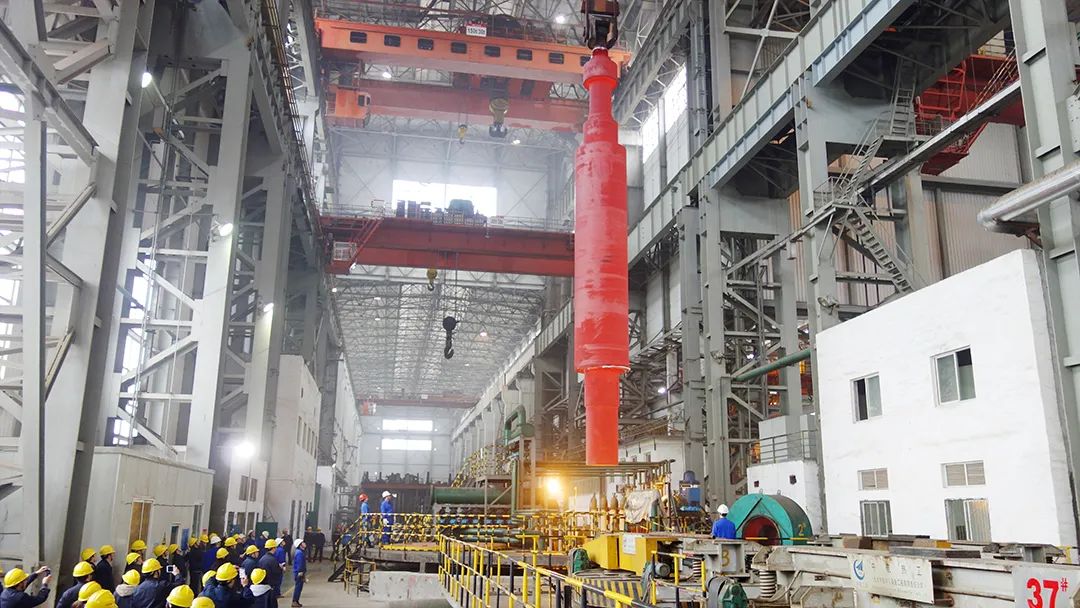
精度之高 质量之优 令人叫绝
2013年8月27日,经过22小时的冶炼、4个大型钢包合浇国和一号发电机转轴锻件钢锭成功。职工们在6个月的生产准备时间里,精心制订和优化了冶炼工艺方案,解决了多项难题。
在进行锻造工序时,车间技术人员和操作人员一起对每个火次的负荷进行详细计算,巧妙研究出一套特殊工装与减重措施,大大降低了起吊和锻造负荷的方法。技术人员牵头,操作人员配合,共同努力研究出一套既有效控制外形尺寸、又确保内部致密性的锻造方法,成功完成国和一号发电机转轴锻件钢锭的锻造。在进行热处理工序时,为琢磨出一套能够有效解决纵、径、切向和心部等不同部位性能热处理的办法,有效避免了淬火应力过大而造成开裂的问题。职工枕戈待旦严格按照工艺技术要求落实各项工艺,对重点环节如装炉、喷淬,做好生产前的冷态演练,最终确保了性能热处理一次合格。在进行机加工序时,广大职工以一丝不苟的工作精神和攻坚克难的工作态度,加班加点,突破创新,成功实现了国和一号核电半速转轴全精加工出产。
在加工过程中,为了保证产品质量,职工们严格履行核电产品操作规程,技术部门加大工艺纪律检查力度,每一道程序都需经过主、副技工互检,技术人员核准,试走刀签字确认后才能执行。重点工序要求必须“精雕细刻”出精品,在满足质量要求的同时必须确保交货期。当用户在现场进行检测时,看见产品形位公差(径向跳动)达到0.002毫米的高精度(比图纸技术要求提高了两三倍)时,不由得赞叹:“还以为你们是磨出来的”。
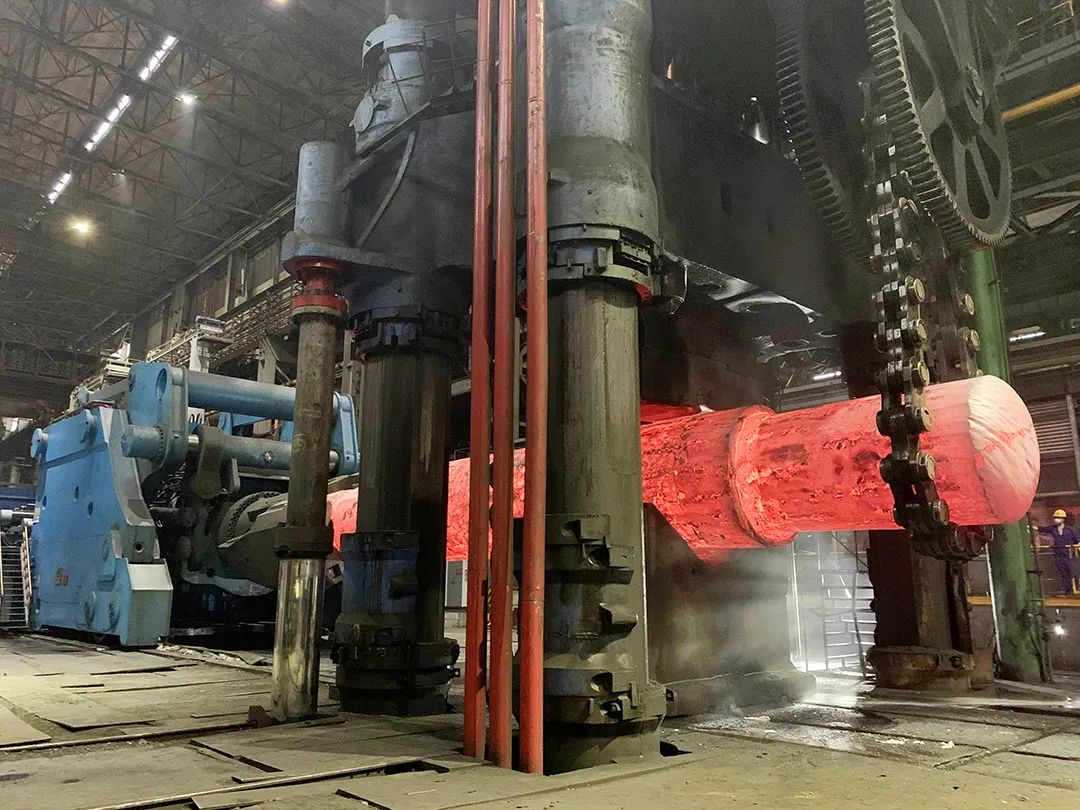
挺起国家核电装备制造的脊梁
从来没有任何一个单件产品需要进行如此细致的系统规划和落实,从来没有一个产品像这个产品一样需要如此多的单位进行协调、穿插配合和备战。通过公司上下共同努力,制定详细的实施技术方案和项目计划,每周对计划完成内容进行逐项落实,最终完美完成了各个工序,产品满足各项技术指标要求,实现零NCR。
国内首支国和一号核电半速转轴锻件的制造,实现了中国核电制造的重大突破,解决了国家核电机组关键部件受制于人的难题,进一步提升了二重在核电大锻件市场的占有率,使其成为公司首屈一指的拳头产品,树立了良好的口碑。
此后,二重连续攻破400至650吨钢锭生产的极限制造技术,先后顺利完成CPR1000、华龙一号等核电项目20余支核电半速转轴的制造任务,充分展现了极限研制能力,成为了世界上少数具备此类高端化、极限化产品制造实力的企业之一。
(二重装备 范林琦 孙嫘 杨耀龙 丁洋/文图 资料图)
来源:二重装备